Solution Spotlight: Expanding Digital Test Capabilities with a Multi-Site Test FeatureFrom Test Connections Newsletter - September 2015
|
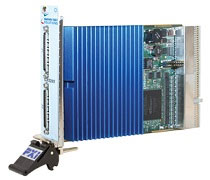
Figure 1: GX5295 |
Today’s semiconductor vendors are increasingly moving to open architecture, PXI –based solutions to provide them with cost effective, compact footprint, and flexible test solutions. MEMS suppliers in particular, are looking to PXI-based solutions as being well-suited for addressing their need for cost effective test solutions. | |
MTS was approached by a major supplier of MEMS devices to help with addressing their requirement to test multiple, low pin count devices using Marvin Test Solutions’ GX5295 digital instrument. Supporting 32 digital channels, with PMU per pin capability, the customer needed to support the testing of 8 devices, using a single GX5295 for their multi-site test configuration. The customer’s key requirements included the following:
- Using the GX5295’s Real-Time Compare function, log the first failure on each channel if/when they occur. The failed channel is correlated to specific site failures.
- For future failure analysis, record the test pattern step where each channel’s first-failure occurred.
- Suppress all further real-time compare operations for a channel, after the first failure.
- Enable or disable first-failure logging on a channel-by-channel basis.
- Support complete test execution, without pause or interruption, regardless of the number of channel failures.
- Report all failed channels with a single register read, avoiding the time-consuming operation of up-loading and post processing the full pattern buffer to identify failed channels.
- Maintain existing real-time compare capability.
- Support the LabVIEW programming environment
With the requirements defined, MTS’ engineering group enhanced the GX5295's features with an updated firmware, driver and software package to meet all of the objectives outlined above. These new features included the following enhancements:
- Channel error latch with a feed-back loop to the real-time compare mask circuit.
- Selection logic to enable the Record-First-Failure (RFF) mode or the standard Real-Time Compare mode (RTC).
- A Channel-Disable register to globally and selectively disable real-time compare per channel when operating in the RFF mode.
- New API functions added to the GX5295 DLL to control the new RFF features
- An upgraded GtDio Panel application which provides interactive control and display of results for the RFF functions
- LabVIEW wrappers for the new RFF functions which were added to the GX5295’s DLL.
ImplementationIn normal operation, the RTC Error Memory will record up to 1K of errors, including address locations. However, for applications that require support for multi-site testing ( and recording of errors on each channel), what is needed is additional control logic that will record only the first failure for each channel, preventing the possibility of overflowing the 1K of error memory if multiple errors occur on a single channel. The block diagram below details the normal RTC operation and the enhanced RFF mode of operation. With the modified GX5295 firmware, both the RTC and RFF features are supported by the module with the mode of operation being a software selection.
Figure 2: RTC and RTF Modes
On-Site Evaluation & DeploymentThe new capabilities were delivered to the customer for beta testing, and installed on a development station in their test lab. The GX5295 supports firmware upgrades in the field by loading the new firmware to the target hardware via the PXI bus. An updated DLL, DioEasy application and updated LabVIEW drivers were also installed on-site.
Initial checkout was done using the DioEasy application and involved loading the GX5295 with test patterns that would guarantee multiple RTC errors across many channels, using a simple loopback cable to inter-connect channels. The original RTC functionality was first demonstrated and verified, proving that the changes did not affect the base-line functionality of the GX5295. Then, the RFF mode was enabled, and the test results verified that only the first failure (and failing vector address) for a channel was recorded in the GX5295 error memory. Subsequent errors for the channel were ignored. At the conclusion of the test, the DioEasy display correctly indicated all known failing channels.
Once the new capabilities were demonstrated, the process was repeated with the customer’s Devices Under Test (DUT’s). The GX5295 executed a 20M-vector scan test on twelve devices simultaneously. With a 1K error memory, the un-enhanced GX5295 would over-run the error memory if one site were bad, forcing a cumbersome coding exercise to monitor the error memory, and when full, save the error information, clear the error memory, and continue the test. At the conclusion of the test, the saved error data had to be integrated and correlated to the failed DUT site(s). With the RFF mode enabled, the tests were again executed and it was verified that only the first failure for a channel was recorded in the GX5295’s error memory. Failures were also induced on several sites, and in each circumstance, the GX5295 correctly identified the failing sites – in a single pass and without an error memory over-run.
The customer’s LabVIEW control program was then modified to add the new functions for setting up and controlling the RFF capabilities and a single “Read Error” VI was placed in parallel with the LabVIEW code that was managing the data collection and correlation to identify failed sites. When executed, the modified code executed as expected and correctly identified all of the failed sites. The end result was that the multi-site test ran faster by eliminating a significant piece of code that was used to manage error collection, reducing a lengthy, iterative process of running, flushing error memory, and restarting the test. In addition, test functionality was improved in that any known bad sites could be excluded from the test simply by writing a value to the Channel Disable Register that would mask the channel associated with that site, eliminating the need to fill a 20M-vector pattern (in this instance) with the equivalent mask pattern. With the enhanced GX5295, MTS was able to deliver a test solution that meets all of the customer’s stated requirements and provides a drop-in upgrade path for those customers using the GX5295 for multi-site semiconductor testing.
|